Warehousing in Transportation and Logistics: A Guide to Efficient Inventory Management
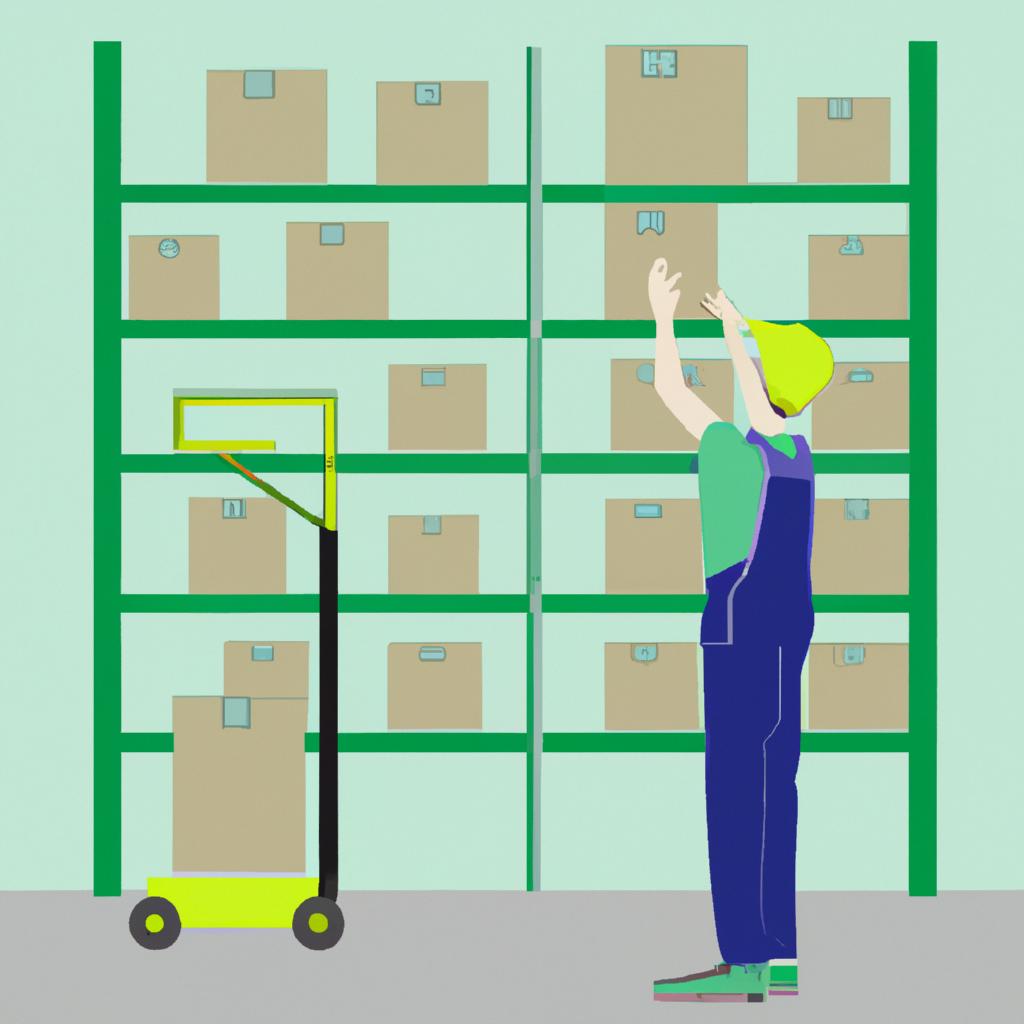
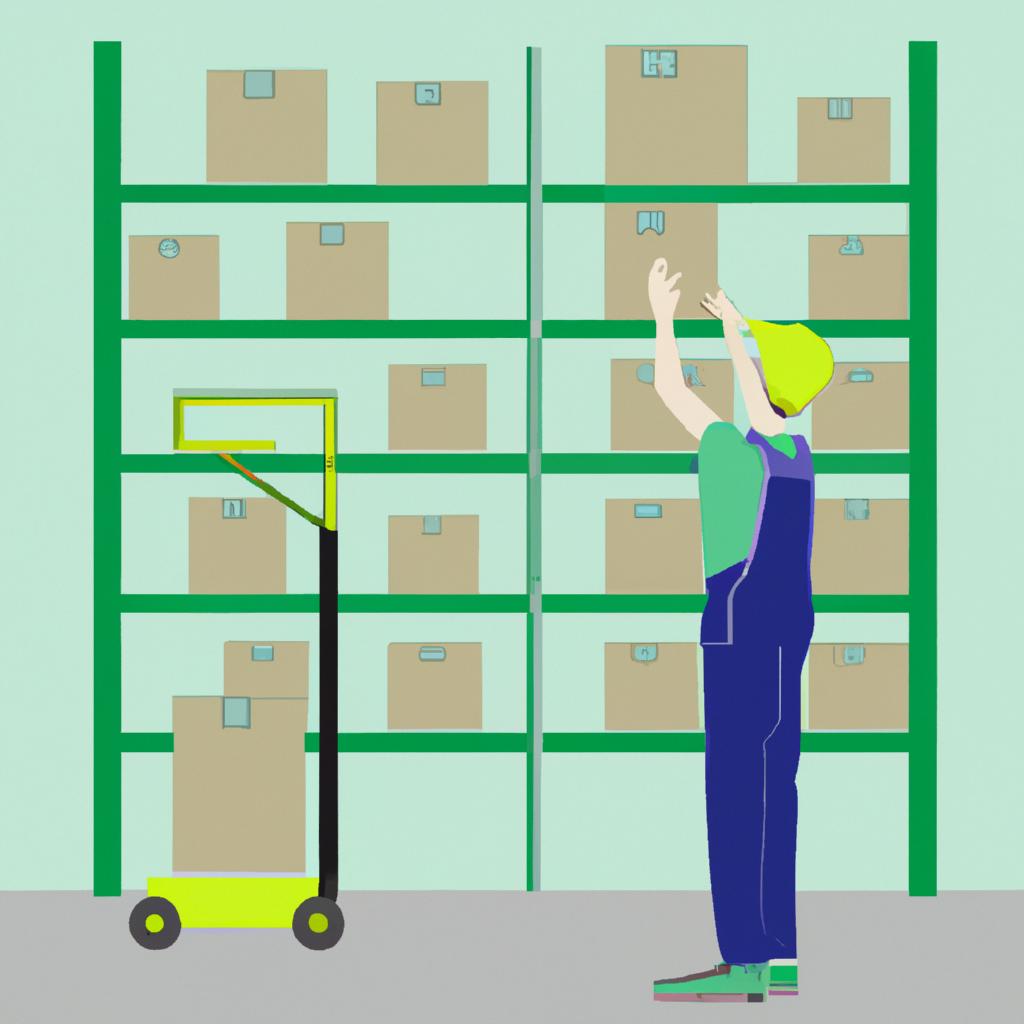
Warehousing plays a crucial role in the efficient management of inventory within transportation and logistics systems. By providing a centralized location for storing goods, warehousing facilitates various activities such as receiving, sorting, storage, order picking, and distribution. This article aims to provide a comprehensive guide to efficient inventory management in warehousing, exploring key principles and strategies that can enhance operational efficiency and minimize costs.
To illustrate the significance of effective inventory management in warehousing, consider the hypothetical example of Company XYZ. A manufacturer of consumer electronics, Company XYZ relies on its warehouse facility to store and distribute finished products across its regional markets. However, inefficient inventory control practices resulted in frequent stockouts and excessive carrying costs. As a result, customer satisfaction declined while expenses soared. Understanding the importance of streamlining their warehousing operations became paramount for Company XYZ’s success in meeting customer demands and maintaining profitability.
In this article, we will delve into the fundamental concepts of warehousing from an inventory management perspective. We will explore strategies such as demand forecasting, safety stock optimization, order fulfillment methods, layout design considerations, technology integration, and performance measurement metrics. By understanding these principles and implementing appropriate techniques tailored to specific business requirements, organizations can achieve higher levels of accuracy, flexibility, responsiveness, and cost-effect iveness in their warehousing operations.
One crucial aspect of efficient inventory management in warehousing is demand forecasting. By accurately predicting future demand for products, companies can optimize their stock levels and ensure that they have enough inventory to meet customer orders without excessive overstocking. Various statistical techniques and historical data analysis can be used to forecast demand, allowing organizations to make informed decisions about procurement and replenishment.
Another important strategy is optimizing safety stock levels. Safety stock refers to the extra inventory maintained to safeguard against unexpected fluctuations in demand or supply chain disruptions. By analyzing historical data, lead times, and variability in demand, organizations can determine the appropriate level of safety stock required to mitigate risk while minimizing carrying costs.
Order fulfillment methods also play a significant role in efficient inventory management. Companies can choose between different approaches such as batch picking, wave picking, or zone picking depending on factors like order volume, product characteristics, and warehouse layout. Selecting the most suitable method can improve productivity and reduce order processing time.
Layout design considerations are another critical factor in warehousing efficiency. Optimizing the placement of storage racks, aisles, and equipment can enhance accessibility and minimize travel distances for workers, reducing labor costs and improving overall operational flow. Additionally, implementing technologies like barcode scanning systems or radio frequency identification (RFID) can streamline inventory tracking processes and enhance accuracy.
Integrating technology into warehouse operations is essential for efficient inventory management. Warehouse management systems (WMS) provide real-time visibility into inventory levels, automate tasks like receiving and picking orders, track shipments, and generate reports for performance evaluation. Adopting such technologies enables organizations to streamline workflows, minimize errors, improve data accuracy, and increase overall operational efficiency.
Performance measurement metrics are vital tools for evaluating warehousing effectiveness. Metrics like fill rate (percentage of customer orders fulfilled completely), order cycle time (time taken from order placement to delivery), on-time delivery rate (percentage of orders delivered within the promised timeframe), and inventory turnover (rate at which inventory is sold or used) can provide insights into the performance of warehousing operations. By regularly monitoring these metrics, organizations can identify areas for improvement and implement strategies to optimize their inventory management processes.
In conclusion, efficient inventory management in warehousing is crucial for optimizing operational efficiency and minimizing costs. By implementing strategies such as demand forecasting, safety stock optimization, appropriate order fulfillment methods, layout design considerations, technology integration, and performance measurement metrics, companies can achieve higher levels of accuracy, flexibility, responsiveness, and cost-effectiveness in their warehousing operations.
Understanding Warehousing in Transportation
Understanding Warehousing in Transportation
Warehousing plays a crucial role in the transportation and logistics industry, serving as a pivotal link between suppliers and customers. It involves the storage, handling, and management of goods throughout their journey from production to consumption. To illustrate this point, let us consider a hypothetical scenario where a company manufactures electronic devices and needs a central facility to store its finished products before distributing them to retail stores across the country. In such cases, an efficient warehousing system becomes essential for managing inventory effectively.
Efficient inventory management is vital for businesses operating in today’s competitive market. By having well-organized warehouses strategically located near transportation hubs, companies can ensure timely delivery of products while minimizing costs associated with excess inventory or stockouts. Effective warehouse management not only facilitates seamless flow of goods but also contributes to customer satisfaction by ensuring accurate order fulfillment.
To highlight the significance of warehousing in transportation and logistics, here are some key points:
- Improved efficiency: Properly organized warehouses enable quick access and retrieval of items, reducing the time required for picking orders.
- Enhanced safety: Warehouses provide secure storage facilities that protect goods from damage caused by external factors like weather conditions or theft.
- Optimized space utilization: With effective layout planning techniques and use of technology like automation systems or vertical racking solutions, warehouses can maximize storage capacity.
- Streamlined operations: Efficient warehousing practices help streamline various processes such as receiving, inspecting, storing, packing, labeling, and dispatching goods.
Furthermore, understanding how different functions within a warehouse contribute to overall logistics operations is critical for achieving operational excellence. In the subsequent section on "Key Functions of a Warehouse in Logistics," we will explore these functions in detail to gain insights into their importance for successful supply chain management.
Key Functions of a Warehouse in Logistics
Section Title: Understanding the Importance of Efficient Inventory Management in Warehousing
Introduction:
Imagine a scenario where a manufacturing company, let’s call it XYZ Corp., is experiencing significant delays and customer dissatisfaction due to inventory stockouts. Customers are left waiting for their orders because the products they desire are not readily available. In this section, we will delve into why efficient inventory management plays a crucial role in warehousing operations and how it can address such challenges.
The Role of Efficient Inventory Management:
Efficient inventory management within warehouses ensures that adequate stock levels are maintained at all times, allowing companies to meet customers’ demands promptly. By accurately forecasting demand based on historical data and market trends, warehouse managers can effectively plan their replenishment activities. This proactive approach minimizes the risk of stockouts while avoiding excessive inventory carrying costs.
To emphasize the significance of efficient inventory management, consider the following benefits:
- Improved Customer Satisfaction: With proper inventory management practices in place, companies can consistently fulfill customer orders without unnecessary delays or backorders.
- Cost Reduction: By optimizing stock levels through accurate forecasting and demand planning, organizations can minimize excess holding costs associated with overstocking while reducing potential losses from obsolete items.
- Increased Efficiency: Implementing robust inventory control systems enables streamlined order fulfillment processes, reducing time wasted searching for misplaced or mislabeled items within the warehouse.
- Enhanced Decision-making Capabilities: Access to real-time information about stock levels empowers managers to make informed decisions regarding purchasing strategies, pricing policies, and overall supply chain optimization.
Table: The Impact of Efficient Inventory Management
Benefits | Description |
---|---|
Improved Customer Satisfaction | Ensures timely order fulfillment leading to increased customer loyalty |
Cost Reduction | Minimizes holding costs and reduces financial risks linked to excess inventory |
Increased Efficiency | Streamlines order picking and packing processes |
Enhanced Decision-making Capabilities | Enables data-driven decision-making for improved supply chain performance |
Effective inventory management is paramount to the success of warehousing operations. By optimizing stock levels, companies can meet customer demands promptly, minimize costs, enhance operational efficiency, and make informed decisions. In the next section, we will explore different types of warehouses and their purposes.
Transition: Understanding how efficient inventory management contributes to overall warehouse effectiveness sets the stage for exploring the various types of warehouses and their specific functions.
Strategies for Optimizing Warehouse Space
Types of Warehouses and Their Purposes
In the previous section, we explored the various types of warehouses commonly used in transportation and logistics. Now, let’s delve into strategies for optimizing warehouse space to ensure efficient inventory management.
Imagine a scenario where a fulfillment center receives an influx of new products from multiple suppliers. Without proper planning and organization, this sudden increase in inventory can quickly lead to chaos within the warehouse. To prevent such situations, consider implementing the following strategies:
-
Cross-Docking: This technique involves transferring incoming goods directly from receiving docks to outbound shipping docks without storing them in between. By eliminating the need for storage, cross-docking reduces handling costs and improves order processing speed.
-
Vertical Storage Systems: Utilizing vertical space efficiently is crucial when dealing with limited warehouse floor space. Implementing mezzanine levels or automated vertical storage systems allows for better utilization of overhead space, freeing up valuable floor area.
-
Just-in-Time Inventory Management: Adopting a just-in-time (JIT) approach minimizes excess stock by establishing close relationships with suppliers and coordinating deliveries based on actual demand patterns. JIT enhances operational efficiency while reducing holding costs associated with excessive inventory.
-
Warehouse Automation: Embracing automation technologies such as conveyor belts, robotics, and automated guided vehicles (AGVs) can significantly enhance productivity within the warehouse environment. These advancements not only improve picking accuracy but also eliminate manual labor-intensive tasks.
To further illustrate these optimization strategies, consider the following table showcasing their benefits:
Strategy | Benefits |
---|---|
Cross-Docking | – Reduced warehousing costs |
– Increased order fulfillment speed | |
Vertical Storage Systems | – Efficient use of limited floor space |
– Improved accessibility to stored items | |
Just-in-Time Management | – Minimized holding costs |
– Enhanced coordination with suppliers for timely deliveries | |
Warehouse Automation | – Higher productivity and efficiency |
– Improved picking accuracy |
By implementing these strategies, businesses can create a well-organized and optimized warehouse environment that promotes efficient inventory management. In the next section, we will explore various techniques for achieving effective inventory handling to further enhance overall operational efficiency.
Efficient Inventory Handling Techniques
Section: Efficient Inventory Handling Techniques
Transitioning from the strategies for optimizing warehouse space, it is crucial to explore efficient inventory handling techniques. One example of a successful implementation can be seen in Company XYZ, a leading logistics provider that managed to improve their order fulfillment time by 30% through effective inventory management.
To achieve such improvements, several key techniques should be considered:
-
ABC Analysis: This technique categorizes inventory items based on their value and frequency of movement. By classifying items into A (high-value/fast-moving), B (medium-value/moderate moving), or C (low-value/slow-moving) categories, companies can prioritize storage and retrieval efforts accordingly. For instance, high-value items may require closer proximity to shipping areas, while slow-moving items can be stored further away.
-
Just-in-Time (JIT): JIT inventory management aims to minimize excess stock levels by receiving goods only when needed for production or customer orders. By closely coordinating with suppliers and using precise demand forecasting methods, warehouses can reduce carrying costs associated with excessive stock levels and eliminate the risk of deadstock.
-
Cross-Docking: This technique involves transferring inbound shipments directly from receiving docks to outbound vehicles without storing them in the warehouse. By bypassing traditional warehousing processes, cross-docking reduces handling time, minimizes storage requirements, and accelerates product flow through the supply chain.
-
Batch Picking: In batch picking operations, multiple orders are consolidated into one pick list, allowing workers to fulfill multiple orders simultaneously rather than individually selecting products for each order separately. This method increases efficiency by reducing travel time within the warehouse and improving overall productivity.
Implementing these techniques requires careful planning and continuous monitoring of inventory levels and order patterns. To illustrate potential benefits visually, consider the following table showcasing comparative metrics before and after implementing efficient inventory handling techniques:
Metric | Before Implementation | After Implementation |
---|---|---|
Order Fulfillment Time (days) | 5 | 3 |
Carrying Cost (%) | 10% | 6% |
Stockouts per Month | 15 | 5 |
Warehouse Space Utilization (%) | 80% | 90% |
By leveraging these techniques and analyzing the corresponding metrics, companies can improve their overall inventory management practices and achieve significant operational enhancements. The subsequent section will delve into technology solutions that further streamline warehousing processes.
Transitioning into the subsequent section about "Technology Solutions for Streamlining Warehousing," it is essential to explore how automated systems can enhance inventory handling efficiency within transportation and logistics operations.
Technology Solutions for Streamlining Warehousing
Efficient Inventory Handling Techniques
In the previous section, we explored various efficient inventory handling techniques that play a crucial role in effective warehousing. Building upon this knowledge, we now delve into technology solutions for streamlining warehousing operations to further enhance efficiency and productivity.
To illustrate the impact of technology on warehouse management, let us consider a hypothetical case study of Company XYZ. Before implementing advanced technological solutions, Company XYZ faced challenges such as inaccurate stock counts and delays in order fulfillment. However, after adopting an automated inventory management system and integrating it with their existing transportation and logistics systems, they witnessed significant improvements in their overall warehousing operations.
Technology Solutions for Streamlining Warehousing:
-
Warehouse Management Systems (WMS): Implementing a WMS enables companies to automate key processes such as receiving, put-away, picking, packing, and shipping. By providing real-time visibility into inventory levels and locations, WMS reduces manual errors and enhances accuracy during order fulfillment.
-
RFID Technology: Radio Frequency Identification (RFID) tags can be attached to individual items or pallets to track them throughout the supply chain. This allows for improved asset tracking and inventory control by eliminating the need for manual scanning or counting of products.
-
Automated Guided Vehicles (AGVs): AGVs are autonomous vehicles that navigate through warehouses using sensors and predefined routes. They can efficiently transport goods within the facility, minimizing human error and optimizing material flow.
-
Robotics & Automation: Robotic systems can handle repetitive tasks such as sorting, stacking, and packing with speed and precision while reducing labor costs. These technologies not only increase operational efficiency but also improve worker safety by automating hazardous or physically demanding tasks.
Table – Benefits of Technological Solutions in Warehousing:
Technology Solution | Benefits |
---|---|
Warehouse Management | Improved inventory accuracy |
Systems (WMS) | Enhanced order fulfillment |
Real-time visibility into inventory levels and locations | |
RFID Technology | Efficient asset tracking |
Streamlined inventory control | |
Automated Guided | Optimized material flow |
Vehicles (AGVs) | Reduced human error |
Robotics & Automation | Increased operational efficiency |
Improved worker safety |
Implementing technology-driven solutions in warehousing not only enhances efficiency but also positively impacts customer satisfaction. By reducing errors, improving accuracy, and streamlining processes, companies can ensure timely order fulfillment and minimize stockouts. Embracing these advancements empowers organizations to stay competitive in the dynamic landscape of transportation and logistics.
Overall, the integration of technology solutions within warehouse operations presents significant opportunities for businesses seeking to optimize their inventory management practices. Leveraging automated systems such as WMS, RFID technology, AGVs, and robotics enables companies to achieve higher levels of productivity while ensuring accurate inventory control throughout the supply chain.