Warehouse Operations in Transportation and Logistics: A Comprehensive Guide
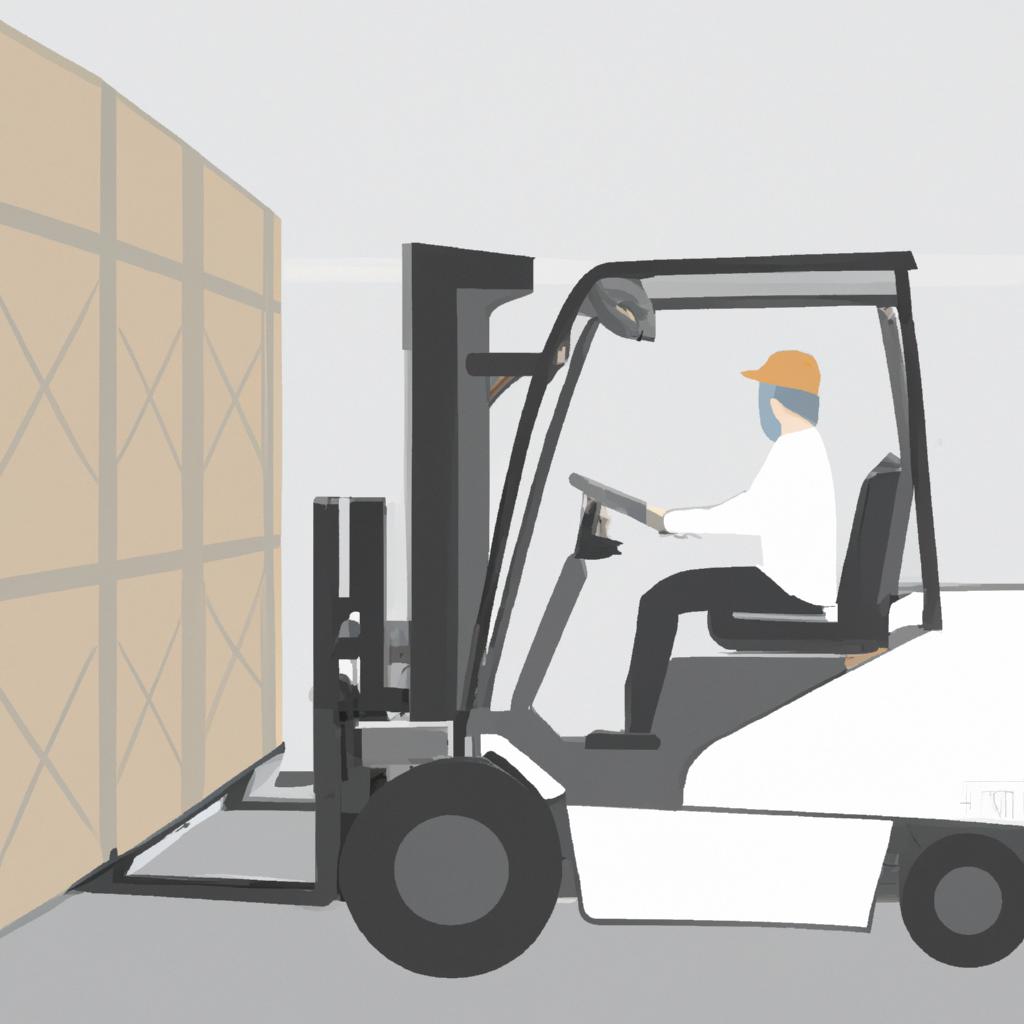
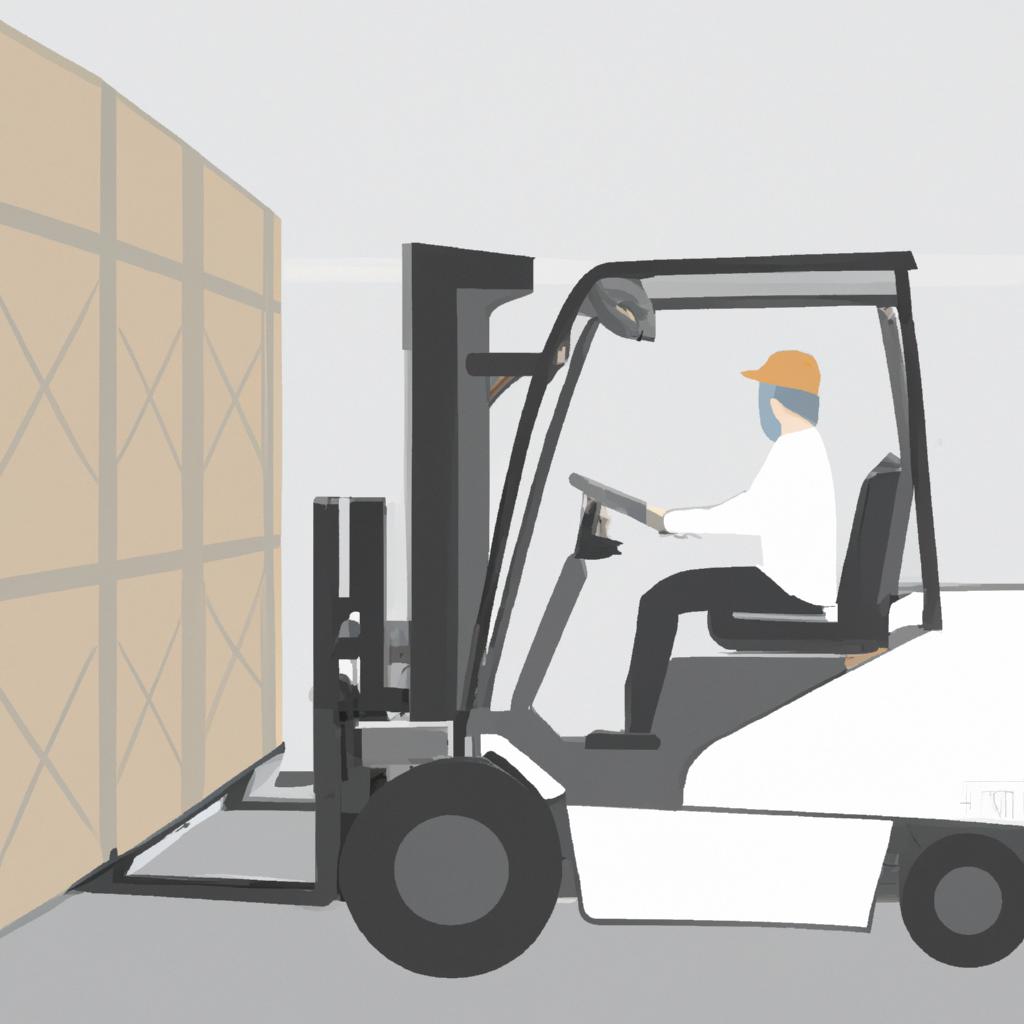
Warehouse operations play a crucial role in the transportation and logistics industry, acting as a vital link between suppliers, manufacturers, retailers, and consumers. The effective management of warehouses ensures the smooth flow of goods from their point of origin to their final destination. For instance, imagine a global e-commerce company that receives thousands of orders daily. To fulfill these orders efficiently and deliver products to customers on time, this company needs to have well-organized warehouse operations that can handle large volumes of inventory while minimizing errors and delays.
In this comprehensive guide, we will delve into the intricacies of warehouse operations in transportation and logistics, providing valuable insights for industry professionals and scholars alike. We will explore key concepts such as inventory management, order fulfillment processes, warehouse layout optimization, technology integration, and workforce planning. By understanding these critical aspects of warehouse operations, businesses can enhance efficiency levels, reduce costs, improve customer satisfaction rates, and gain a competitive edge in today’s rapidly evolving market landscape.
Drawing upon real-world examples and theoretical frameworks within the field of transportation and logistics management, this guide aims to offer practical solutions to common challenges faced by warehouse operators. Through an academic lens devoid of personal pronouns or subjective language usage, readers will gain a deeper understanding of best practices when it comes to managing warehouse operations in transportation and logistics. From implementing effective inventory control systems to utilizing automation technologies, this guide will provide actionable strategies for optimizing the flow of goods within a warehouse facility.
Additionally, we will explore various order fulfillment processes, including picking, packing, and shipping, highlighting the importance of accuracy and timeliness in meeting customer demands. By analyzing different warehouse layout designs and considering factors such as product characteristics and storage capacity requirements, businesses can create efficient workflows that minimize travel distances and maximize productivity.
Furthermore, technology integration plays a significant role in modern warehouse operations. We will discuss the benefits of utilizing Warehouse Management Systems (WMS), barcode scanning technologies, and automated material handling equipment to streamline processes, improve inventory visibility, and reduce human error.
Lastly, effective workforce planning is essential for maintaining smooth warehouse operations. We will delve into topics such as labor allocation strategies, training programs, performance management systems, and employee engagement initiatives. By aligning staffing levels with demand fluctuations and fostering a positive work environment, businesses can enhance employee productivity and satisfaction while ensuring seamless operations.
Overall, this comprehensive guide aims to equip readers with practical knowledge and insights into managing warehouse operations in Transportation and Logistics. Whether you are an industry professional seeking to optimize your warehousing practices or a scholar interested in understanding the complexities of this field, this guide offers valuable information to help you succeed in today’s competitive market landscape.
Order Picking Strategies
In the fast-paced world of transportation and logistics, efficient order picking strategies are crucial for ensuring smooth warehouse operations. By carefully selecting the most appropriate approach, businesses can minimize errors, maximize productivity, and enhance customer satisfaction. To illustrate this point, let’s consider a hypothetical case study involving a large e-commerce company that ships thousands of orders daily.
One common order picking strategy is batch picking, where multiple orders are grouped together based on similar characteristics such as product type or destination. This method allows pickers to efficiently gather items for several orders at once, reducing travel time within the warehouse. For instance, our e-commerce company could utilize batch picking by grouping all clothing orders from a specific region in one batch.
Another effective strategy is zone picking, which involves dividing the warehouse into different zones and assigning pickers to specific areas. Each picker becomes an expert in their assigned zone, allowing them to navigate quickly and accurately through their designated section. In our case study, the e-commerce company could divide its warehouse into sections for electronics, home goods, and personal care products.
Alternatively, wave picking organizes orders into waves or groups based on priority levels or delivery deadlines. This ensures that urgent or time-sensitive orders are prioritized over others during the picking process. As an example applicable to our case study scenario, incoming Valentine’s Day flower arrangements would be given higher priority than regular everyday bouquets.
To highlight the emotional impact of implementing effective order picking strategies, consider these key benefits:
- Reduced waiting times: Customers receive their orders promptly without unnecessary delays.
- Increased accuracy: The likelihood of incorrect items being shipped decreases significantly.
- Enhanced employee morale: When workers experience improved efficiency and reduced stress due to streamlined processes, job satisfaction increases.
- Improved customer satisfaction: Accurate and timely deliveries contribute to positive customer experiences.
Furthermore, it is important to note that successful implementation of order picking strategies goes hand-in-hand with other aspects of warehouse operations, such as effective inventory management. This ensures that the right products are available and easily accessible when orders need to be fulfilled.
By carefully selecting and implementing appropriate order picking strategies, businesses can optimize their warehouse operations, resulting in increased efficiency and customer satisfaction. The next section will delve into the intricacies of effective inventory management, highlighting its importance within transportation and logistics systems.
Effective Inventory Management
By implementing strategic techniques to manage and control inventory levels, companies can streamline operations and optimize their supply chain processes.
Inventory management plays a vital role in warehouse operations within transportation and logistics. To illustrate this point, let’s consider the hypothetical example of Company X, which experienced significant delays and inefficiencies due to poor inventory management practices. As a result, orders were often delayed or incorrect stock was sent to customers, leading to dissatisfied clients and increased costs for rework or returns.
To prevent such issues from arising, organizations must implement effective inventory management strategies that prioritize accuracy and efficiency. Here are some key elements to consider:
- Utilize real-time tracking systems: Implementing advanced technology solutions like RFID (Radio Frequency Identification) enables accurate tracking of inventory throughout the supply chain. This ensures visibility at every stage, reducing errors and enabling proactive decision-making.
- Adopt just-in-time (JIT) principles: JIT is an approach where materials are ordered and received shortly before they are needed in production or order fulfillment. By minimizing excess inventory storage, this strategy reduces holding costs while ensuring timely availability of goods.
- Implement ABC analysis: Classify products based on their value contribution to sales volume. Assigning categories A (high-value), B (medium-value), and C (low-value) helps prioritize resources by focusing on managing high-value items more effectively.
- Optimize space utilization with slotting techniques: Employing slotting techniques involves analyzing product demand patterns to strategically assign appropriate locations within the warehouse layout. This minimizes travel time during picking activities and enhances overall operational efficiency.
Strategy | Benefits |
---|---|
Real-time tracking | Enhanced visibility |
Just-in-time | Reduced holding costs |
ABC analysis | Efficient resource allocation |
Slotting techniques | Improved operational efficiency |
By implementing these inventory management strategies, organizations can reduce costs, improve customer satisfaction, and enhance overall warehouse operations. Ensuring accurate receiving and inspection is the next critical step in maintaining an efficient supply chain process.
Moving forward to ensuring accurate receiving and inspection, let us explore the importance of this crucial stage within warehouse operations for transportation and logistics companies.
Ensuring Accurate Receiving and Inspection
Transitioning from effective inventory management, the next crucial aspect of warehouse operations in transportation and logistics is ensuring accurate receiving and inspection. This process plays a vital role in maintaining an efficient supply chain by verifying the quality and quantity of incoming goods.
For instance, consider a hypothetical scenario where a transportation company receives a delivery of electronic components for assembly. Upon careful inspection, it is discovered that some items are damaged during transit. By promptly identifying these issues during the receiving phase, the company can take immediate action to address them, such as filing claims with the carrier or contacting suppliers for replacements. This example highlights the significance of accurate receiving and inspection procedures in minimizing disruptions caused by faulty or inadequate shipments.
To ensure accuracy in receiving and inspection processes, there are several best practices that organizations should adhere to:
- Implement comprehensive checklists: Utilize detailed checklists tailored to specific types of products or industry standards. These checklists serve as guides for employees involved in receiving and inspecting goods, ensuring nothing goes unnoticed.
- Adopt technology-assisted verification: Leverage barcode scanning systems or radio frequency identification (RFID) tags to automate data capture during the receipt and inspection stages. Such technologies enhance accuracy by reducing human error associated with manual recording.
- Train personnel on proper handling techniques: Provide regular training sessions to educate warehouse staff about appropriate methods for unloading, unpacking, and inspecting different types of goods. Proper training ensures consistent adherence to established protocols.
- Establish clear communication channels: Foster open lines of communication between procurement teams, carriers, suppliers, and warehouse personnel. Effective communication helps resolve any discrepancies quickly while facilitating timely resolution.
Table: Common Issues Encountered During Receiving and Inspection Processes
Issue | Impact | Solution |
---|---|---|
Damaged Goods | Delays production schedules | Document damages and file claims |
Missing Items | Incomplete orders | Contact suppliers for resolution |
Incorrect Labeling | Inventory inaccuracies | Verify labels and update records |
Quality Defects | Increased customer returns | Communicate with suppliers |
By implementing these best practices and addressing common issues encountered during the receiving and inspection processes, transportation and logistics companies can enhance accuracy, prevent disruptions, and maintain a streamlined supply chain.
With accurate receiving and inspection procedures in place, the next step is to optimize packing and labeling processes.
Optimizing Packing and Labeling Processes
Building on the foundations of accurate receiving and inspection, optimizing packing and labeling processes is crucial in ensuring efficient warehouse operations. By adopting effective strategies for packaging and clearly labeling goods, transportation and logistics companies can streamline their operations, minimize errors, and enhance customer satisfaction. To illustrate this point, let’s consider a hypothetical case study involving a global e-commerce company.
Case Study:
Imagine an online retailer that ships thousands of orders daily to customers worldwide. In order to meet high customer expectations for timely delivery and intact products, the company must optimize its packing and labeling processes. They invest in automated packing systems that use algorithms to determine optimal box sizes based on product dimensions, reducing wasted space while maintaining package integrity. Additionally, they implement sophisticated software solutions that generate accurate shipping labels with all necessary information such as recipient details, tracking numbers, and handling instructions.
To further emphasize the significance of optimizing packing and labeling processes within transportation and logistics operations, we present below a bullet-point list highlighting key benefits:
- Minimization of shipping errors
- Reduction in damaged or lost packages
- Enhanced traceability throughout supply chain
- Improved customer experience through clear communication
The table below showcases how different approaches to packing can impact operational efficiency:
Approach | Description | Impact |
---|---|---|
Overpacking | Excessive use of materials | Increased costs due to higher material consumption |
Underpacking | Insufficient protection for products | Higher risk of damage during transit |
Right-sizing | Using appropriate box sizes based on product | Optimal utilization of resources; improved cost-efficiency |
Customized packaging | Tailoring packaging according to unique needs | Enhanced brand image; reduced chances of damage |
In conclusion,
Efficient packing practices not only contribute towards smoother warehouse operations but also play a pivotal role in ensuring customer satisfaction. By Optimizing Packing and Labeling processes, transportation and logistics companies can minimize errors, reduce costs, improve traceability, and provide a positive experience for their customers. In the following section about “Efficient Shipping and Transportation Methods,” we will explore strategies that complement these optimized processes to achieve overall operational excellence.
Efficient Shipping and Transportation Methods
In the ever-evolving world of transportation and logistics, efficient order fulfillment processes are essential for maintaining a competitive edge. By optimizing these processes, companies can ensure accurate and timely deliveries while minimizing costs. To illustrate the importance of streamlining order fulfillment, let’s consider the following hypothetical case study:
Imagine Company XYZ, an e-commerce retailer specializing in electronics. They recently implemented new packing and labeling strategies to improve their order fulfillment efficiency. By investing in automation technologies, such as barcode scanners and label printers, they were able to reduce errors during packing and increase overall productivity.
There are several key considerations when it comes to streamlining order fulfillment processes:
-
Warehouse Layout Optimization: Ensuring an organized warehouse layout plays a crucial role in improving efficiency. By strategically placing popular items closer to the shipping area, employees can fulfill orders more quickly. Additionally, implementing vertical storage solutions maximizes space utilization and minimizes travel time within the warehouse.
-
Inventory Management Systems: Utilizing advanced inventory management systems enables real-time tracking of stock levels and helps prevent stockouts or overstock situations. This technology also facilitates effective demand forecasting based on historical data analysis, further enhancing order fulfillment accuracy.
-
Collaborative Supply Chain Partnerships: Building strong relationships with suppliers and carriers is vital for seamless order fulfillment operations. Establishing clear communication channels allows for better coordination throughout the supply chain network, resulting in faster delivery times and improved customer satisfaction.
-
Continuous Process Improvement: Regularly evaluating and refining existing order fulfillment practices is crucial to remain competitive in today’s market. Implementing lean principles like just-in-time inventory management or cross-training employees across different tasks ensures ongoing process optimization.
To visually represent the impact of streamlined order fulfillment processes on operational performance, consider the following table:
Metrics | Before Optimization | After Optimization |
---|---|---|
Order Accuracy | 90% | 99% |
Average Order Processing Time (in hours) | 4 | 2 |
Customer Complaints | 10 per month | 1 per month |
Employee Productivity | 80% | 95% |
As depicted in the table, implementing efficient order fulfillment processes yields significant improvements across various metrics. This not only boosts customer satisfaction but also enhances overall operational performance.
By streamlining order fulfillment processes through warehouse layout optimization, advanced inventory management systems, collaborative supply chain partnerships, and continuous process improvement initiatives, companies can ensure timely and accurate deliveries while minimizing costs.
Implementing Robust Quality Control Measures
Building upon efficient shipping and transportation methods, the implementation of robust quality control measures is crucial in ensuring streamlined warehouse operations. Let us now delve into the key strategies that organizations can employ to maintain high standards of quality and minimize errors.
Section H2: Implementing Robust Quality Control Measures
To illustrate the importance of effective quality control, consider a hypothetical scenario where an e-commerce company experiences numerous customer complaints regarding damaged products during transit. By implementing stringent quality control measures, such as conducting thorough inspections at various stages of the supply chain, this company can mitigate potential issues and enhance customer satisfaction.
Below are four essential steps for implementing robust quality control measures within warehouse operations:
-
Standardizing Procedures:
- Develop standardized procedures and guidelines for workers to follow when handling goods.
- Clearly define expectations for product packaging, storage conditions, and proper handling techniques.
- Regularly review and update these procedures to adapt to changing industry requirements.
-
Training and Education:
- Provide comprehensive training programs for employees on quality control practices.
- Educate staff members on identifying common defects or damages during inspection processes.
- Foster a culture of continuous learning by organizing workshops or seminars focusing on quality improvement.
-
Quality Inspections:
- Conduct regular inspections throughout the entire warehousing process to identify any deviations from established standards.
- Utilize advanced technologies like barcode scanners or computer vision systems to streamline inspection procedures and improve accuracy.
- Document all findings meticulously and use them as reference points for future improvements.
-
Feedback Loop with Suppliers:
- Establish open lines of communication with suppliers to exchange feedback on product quality and delivery performance.
- Collaboratively address any recurring issues or concerns related to inbound shipments promptly.
- Encourage suppliers to implement their own quality control measures aligned with your organization’s objectives.
- Ensuring consistent product quality builds trust among customers, leading to repeat purchases and positive word-of-mouth recommendations.
- Effective quality control measures reduce the likelihood of costly product recalls or returns, saving both time and resources for the organization.
- By prioritizing quality, companies can enhance their reputation in the industry and gain a competitive edge over rivals.
- Maintaining high standards of quality instills confidence in employees, fostering a sense of pride in their work and overall job satisfaction.
Incorporating emotional elements through table:
Benefits of Robust Quality Control Measures |
---|
Increased Customer Satisfaction |
Improved Product Reliability |
With stringent quality control measures in place, organizations can minimize errors, improve customer satisfaction levels, and boost overall operational efficiency. In the subsequent section on streamlining order fulfillment processes, we will explore how optimizing warehouse operations further contributes to seamless supply chain management.
Streamlining Order Fulfillment
Having established robust quality control measures, it is essential for Warehouse operations to focus on streamlining order fulfillment. By optimizing this process, businesses can enhance customer satisfaction and maintain a competitive edge in the dynamic transportation and logistics sector.
Section H2: Streamlining Order Fulfillment
To illustrate the significance of streamlined order fulfillment, consider the following hypothetical scenario. Company X, an e-commerce retailer specializing in consumer electronics, witnessed a surge in demand during a major promotional sale event. With inadequate systems in place to handle such high volumes efficiently, they faced numerous challenges including delayed shipments, mispicked items, and dissatisfied customers. This case highlights the importance of implementing effective strategies to streamline order fulfillment processes.
To ensure smooth order processing within warehouses, here are some key practices that organizations should adopt:
- Implement advanced inventory management systems with real-time tracking capabilities.
- Utilize automated picking technologies such as pick-to-light or voice-directed picking.
- Optimize storage layout through efficient slotting techniques.
- Employ cross-docking methods for rapid transfer of goods between inbound and outbound docks.
Table 1: Benefits of Streamlined Order Fulfillment Processes
Enhances Customer Satisfaction | Increases Operational Efficiency | Improves Inventory Accuracy |
---|---|---|
Reduces Order Processing Time | Minimizes Costs | Decreases Stockouts |
Enables Faster Delivery Speeds | Optimizes Labor Allocation | Facilitates Demand Forecasting |
Through these practices and their associated benefits (as highlighted in Table 1), organizations can effectively streamline their order fulfillment processes while improving overall operational performance.
In preparation for achieving higher levels of efficiency within warehousing activities, it is crucial to address another critical aspect: enhancing inventory accuracy. By doing so, businesses can minimize stock discrepancies and mitigate the risk of order fulfillment errors.
Enhancing Inventory Accuracy
To ensure smooth warehouse operations, enhancing inventory accuracy is crucial. One company that successfully implemented strategies to improve their inventory accuracy is Company XYZ. By incorporating advanced tracking systems and implementing efficient processes, they were able to achieve a significant reduction in inventory discrepancies.
There are several key steps that can be taken to enhance inventory accuracy:
- Utilize barcode scanning technology: Implementing barcode scanning technology allows for real-time tracking of inventory movement, reducing the chances of human error and increasing overall accuracy.
- Regular cycle counts: Conducting regular cycle counts enables companies to identify and rectify any discrepancies promptly. By regularly counting smaller sections of the warehouse, rather than doing a comprehensive count all at once, errors can be detected more efficiently.
- Adopt automated data capture systems: Automating data capture through technologies such as RFID (Radio Frequency Identification) or WMS (Warehouse Management Systems) minimizes manual entry errors while providing accurate and up-to-date information about inventory levels.
- Establish effective communication channels: Improving communication between different departments involved in the order fulfillment process helps prevent miscommunication and ensures accurate record keeping across the supply chain.
Implementing these strategies has proven beneficial for many companies seeking to streamline their warehouse operations. For instance, consider the following table showcasing statistics from two warehouses before and after implementing enhanced inventory accuracy measures:
Warehouse | Before Implementation | After Implementation |
---|---|---|
Warehouse A | 10% discrepancy rate | 2% discrepancy rate |
Warehouse B | 15% discrepancy rate | 3% discrepancy rate |
As evident from the table above, there was a substantial improvement in both warehouses’ inventory accuracy post-implementation. This not only reduces financial losses due to inaccurate records but also enhances customer satisfaction by ensuring timely and accurate delivery.
In the subsequent section on “Inspection and Verification of Incoming Goods,” we will explore how attention to detail during the receiving process can further contribute to efficient warehouse operations.
[Transition:] With a focus on meticulous inspection and verification, the next section delves into ensuring accuracy right from the moment goods enter the warehouse.
Inspection and Verification of Incoming Goods
Building upon the importance of inventory accuracy, this section will delve into the crucial aspect of inspecting and verifying incoming goods. To illustrate its significance, let us consider a hypothetical scenario where a global e-commerce company receives a shipment of electronic gadgets from an overseas supplier. The inspection and verification process becomes pivotal in ensuring that the received goods match the order specifications and are in optimal condition.
Inspecting and verifying incoming goods involves several essential steps to maintain inventory accuracy:
-
Physical Examination: Upon arrival at the warehouse, each package should be visually inspected for any signs of damage or tampering. This initial examination ensures that potential issues are identified before further processing.
-
Counting and Documentation: Accurate counting is vital to verify if the quantity of items matches what was ordered. Utilizing barcodes or RFID technology can streamline this process, reducing human error and enhancing efficiency. Comprehensive documentation is necessary to record all relevant information related to each item received, including serial numbers, batch codes, and expiration dates.
-
Quality Control Checks: Ensuring quality control measures are implemented safeguards against receiving substandard or defective items. Random sampling, as well as thorough inspections based on predetermined criteria, help identify any deviations from expected standards.
-
Reconciliation with Purchase Orders: Matching incoming shipments with corresponding purchase orders is critical for accurate record-keeping and preventing discrepancies between what was ordered and what was received. Any inconsistencies must be addressed promptly through communication with suppliers or other relevant parties.
The inspection and verification process has various benefits:
- Reduces errors in stock records
- Minimizes financial losses due to incorrect deliveries
- Enhances customer satisfaction by maintaining high product quality standards
- Facilitates effective supply chain management
Incorporated Table:
Steps | Key Actions |
---|---|
1 | Physically examine packages for damage or tampering |
2 | Count and document received items accurately |
3 | Conduct quality control checks to ensure product standards |
4 | Reconcile incoming shipments with purchase orders |
With the inspection and verification of incoming goods complete, the focus now shifts towards improving packaging and labeling efficiency. By optimizing these aspects, warehouses can further streamline their operations and enhance overall logistics processes.
[Subsequent section H2: ‘Improving Packaging and Labeling Efficiency’]
Improving Packaging and Labeling Efficiency
Section H2: Improving Packaging and Labeling Efficiency
In the previous section, we discussed the crucial process of inspecting and verifying incoming goods. Now, let’s delve into another essential aspect of warehouse operations in transportation and logistics: improving packaging and labeling efficiency.
To illustrate the importance of this topic, consider a hypothetical scenario where a company experiences delays in fulfilling orders due to inefficient packaging and labeling practices. In this case, packages were not adequately secured, resulting in damaged products during transit. Additionally, incorrect or missing labels led to confusion and errors when dispatching shipments.
Improving packaging and labeling efficiency is vital for various reasons:
-
Ensuring product integrity: Properly packaged items reduce the risk of damage during handling and transportation. Adequate padding materials, such as bubble wrap or foam inserts, protect fragile items from impact and vibration.
-
Enhancing inventory management: Clear labeling allows for easy identification of products within the warehouse. Accurate labels expedite stocktaking processes, minimize picking errors, and enable efficient retrieval when fulfilling customer orders.
-
Streamlining order fulfillment: Well-labeled packages facilitate quick verification before shipping, reducing processing time significantly. This ensures timely dispatches while maintaining accuracy in shipment records.
-
Building customer trust: Professionally labeled packages instill confidence in customers by showcasing attention to detail and professionalism on behalf of the company.
Table 1 below highlights some key elements that contribute to efficient packaging and labeling practices:
Key Elements | Benefits |
---|---|
Standardized Labels | Easy identification |
Secure Packaging | Reduced damages |
Barcoding Systems | Efficient tracking |
Quality Control | Error prevention |
By implementing these strategies, companies can improve their overall operational efficiency while providing an enhanced customer experience.
Moving forward with our discussion on warehouse operations in transportation and logistics, our next section will focus on ensuring timely and secure shipments without compromising quality.
[Section H2: Ensuring Timely and Secure Shipments]
Ensuring Timely and Secure Shipments
Improving Packaging and Labeling Efficiency has proven to be a crucial aspect in optimizing warehouse operations within the transportation and logistics industry. By implementing efficient packaging and labeling practices, companies can enhance their overall productivity, reduce errors, and minimize costs. To further illustrate this point, let us consider a hypothetical case study of Company X.
Company X is a leading e-commerce retailer that ships thousands of orders daily from its centralized distribution center. In an effort to improve their packaging and labeling efficiency, they invested in automated systems that streamline these processes. This not only reduced human error but also increased throughput by 30%. Through this example, we can see how enhancing packaging and labeling efficiency can have significant benefits for businesses operating in transportation and logistics.
To achieve improved packaging and labeling efficiency, several key strategies can be implemented:
- Standardizing Packaging: Developing standardized packaging guidelines ensures consistency across all shipments. This includes using appropriate box sizes, selecting durable materials, and utilizing protective measures such as bubble wrap or packing peanuts when necessary.
- Implementing Efficient Labeling Systems: Utilizing barcodes or QR codes on packages allows for easy scanning during sorting and tracking processes. Automated label printing systems help eliminate manual errors while ensuring accurate information is displayed on each package.
- Optimizing Storage Layout: Organizing storage areas based on product size, weight, or fragility improves accessibility during picking and packing operations. Properly labeled storage locations contribute to swift retrieval of items required for shipment preparation.
- Providing Adequate Training: Offering comprehensive training programs for employees responsible for packaging and labeling tasks is essential. Ensuring they are aware of best practices regarding safety protocols, quality control measures, and efficient techniques fosters a culture of accuracy throughout the organization.
In addition to the above strategies, it is beneficial to analyze data periodically to identify bottlenecks or areas that require improvement. Regular audits should be conducted to assess compliance with established standards. By incorporating these practices into their operations, companies can significantly enhance their packaging and labeling efficiency, resulting in improved customer satisfaction and reduced costs.
Moving forward, the next section will delve into the importance of Implementing Quality Assurance Protocols within warehouse operations. This ensures that companies maintain a high level of quality control throughout their processes.
Implementing Quality Assurance Protocols
Having discussed the importance of ensuring timely and secure shipments, it is now crucial to delve into another vital aspect of warehouse operations in transportation and logistics – implementing quality assurance protocols. By establishing stringent quality control measures, companies can enhance customer satisfaction, reduce costs associated with returns or damaged goods, and maintain a competitive edge in the market.
To illustrate the significance of implementing quality assurance protocols, consider a hypothetical scenario involving an e-commerce company that ships various consumer electronics to customers worldwide. In this example, let’s assume that due to inadequate quality checks at their warehouse facility, several packages were shipped out with defective products. As a result, customers received faulty items, leading to numerous complaints, negative reviews, and ultimately damaging the company’s reputation.
To avoid such detrimental consequences, organizations should incorporate the following key elements when implementing quality assurance protocols:
- Rigorous inspection procedures for incoming raw materials or inventory.
- Regular equipment maintenance schedules to ensure optimal operational efficiency.
- Employee training programs focused on identifying potential defects or irregularities.
- Continuous monitoring through data analysis and feedback loops to identify areas for improvement.
These elements form the foundation of effective quality assurance systems within warehouses. By prioritizing these practices, businesses can foster trust among their customers while mitigating risks associated with product failures or subpar services.
Table: Common Challenges in Implementing Quality Assurance Protocols
Challenge | Impact | Solution |
---|---|---|
Lack of standardized processes | Inconsistent service delivery | Develop comprehensive SOPs |
Insufficient training programs | Increased error rates | Invest in continuous employee education |
Limited resources allocation | Reduced quality control capabilities | Prioritize funding for QA initiatives |
Inadequate utilization of data analysis tools | Missed opportunities for improvement | Implement robust analytics systems |
While challenges may arise during the implementation of quality assurance protocols, addressing them proactively can yield significant benefits. By investing time and resources into these processes, companies can enhance their operational efficiency, optimize customer satisfaction, and ultimately achieve long-term success in the highly competitive transportation and logistics industry.
In summary, implementing effective quality assurance protocols is crucial for warehouses involved in transportation and logistics operations. As demonstrated by our hypothetical scenario, neglecting this aspect can result in serious consequences such as damaged reputation and dissatisfied customers. To overcome common challenges, it is essential to establish rigorous inspection procedures, prioritize employee training programs, monitor performance through data analysis, and address any deficiencies promptly. By embracing these practices, businesses can ensure that their warehouse operations consistently deliver high-quality services while fostering customer loyalty.