Packing and Labeling in Transportation and Logistics: Warehouse Operations
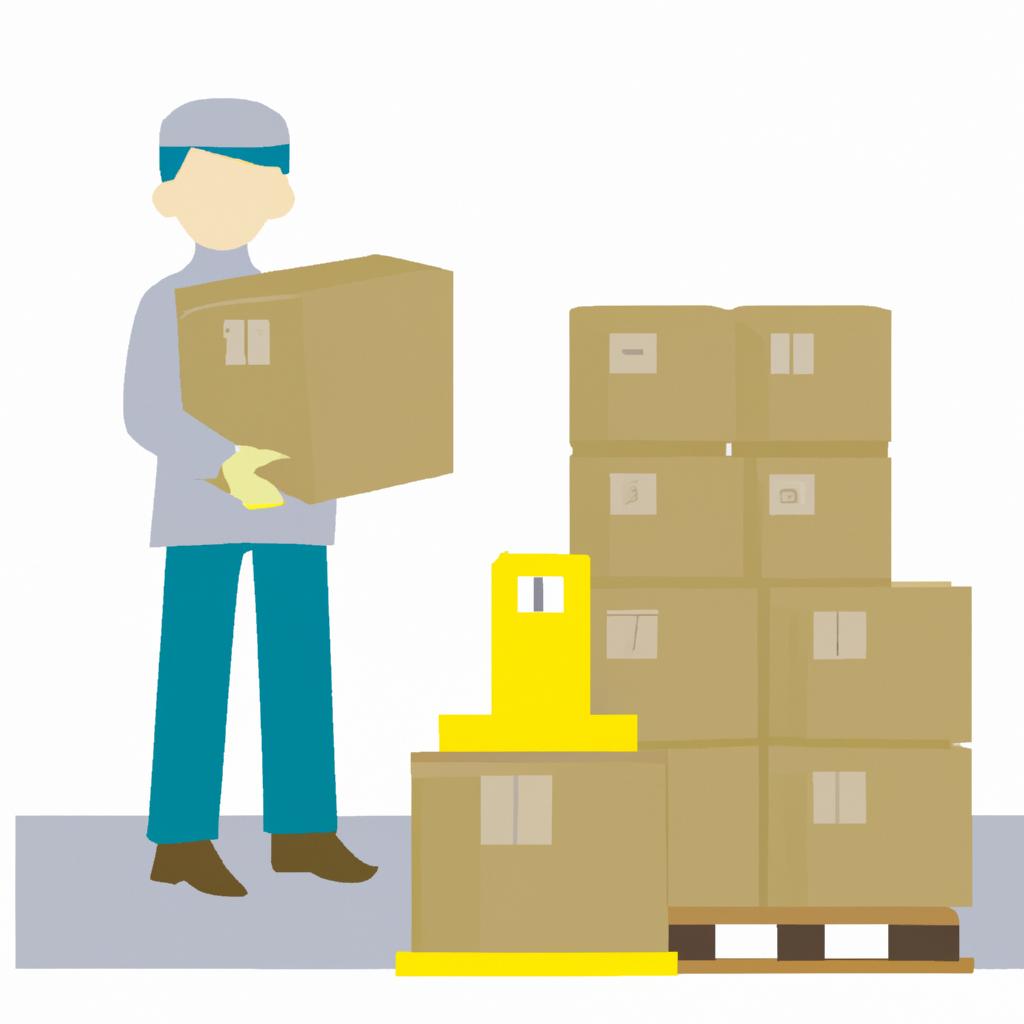
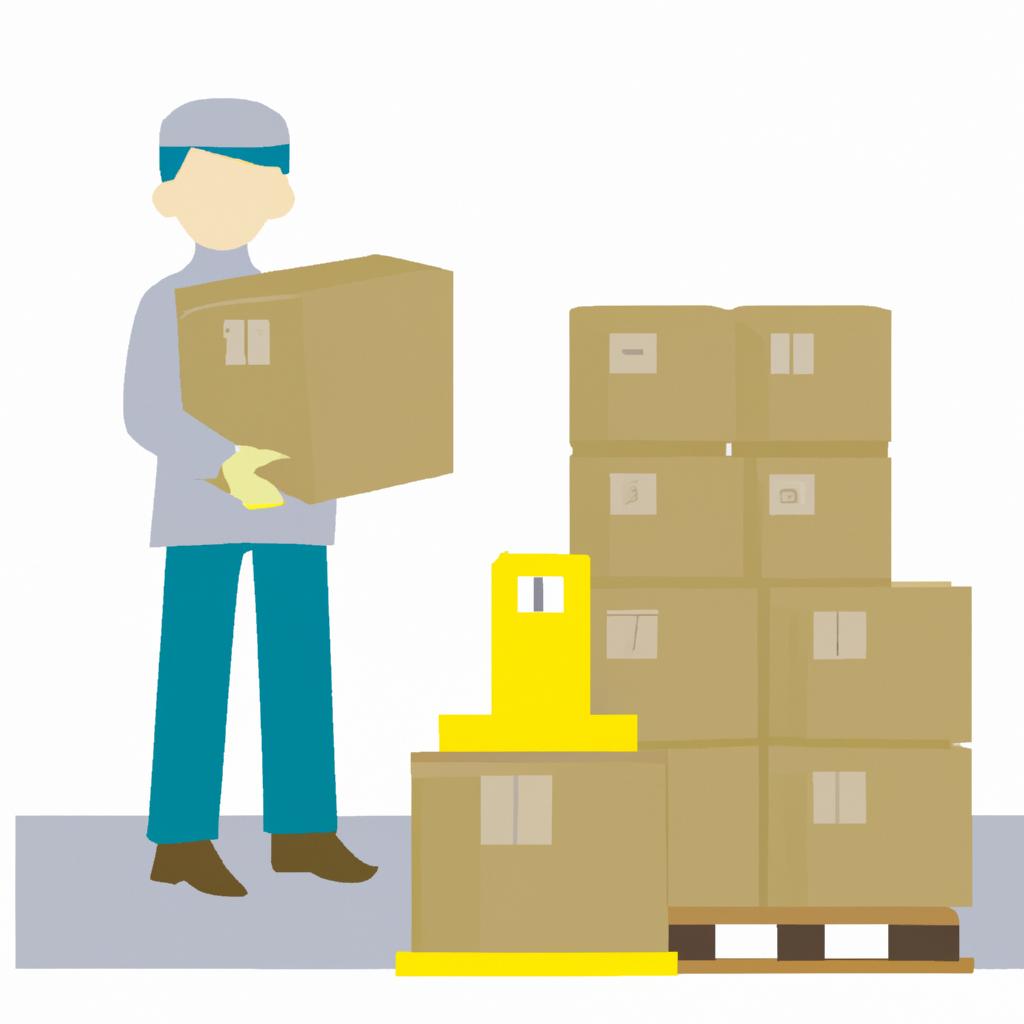
The efficient and organized management of packing and labeling in transportation and logistics is essential for smooth warehouse operations. This article delves into the significance of effective packing and labeling practices within the context of warehouse operations, highlighting their impact on inventory control, order accuracy, and customer satisfaction. To illustrate this point, let us consider a hypothetical case study: Company XYZ operates a large distribution center that receives thousands of products daily from various suppliers. Without proper packing and labeling protocols in place, it becomes increasingly challenging to identify, sort, and store these products efficiently.
In today’s fast-paced global marketplace, where time is of the essence, businesses rely heavily on an intricately designed network of warehouses to ensure timely delivery and optimal product availability. The process of packing involves carefully arranging goods into suitable containers or packaging materials based on factors such as size, weight, fragility, and type. Simultaneously, labeling plays a crucial role by providing vital information about the contents inside each package – including product details like SKU numbers, descriptions, barcodes/QR codes – facilitating easy identification throughout the supply chain. By adhering to standardized packing techniques and implementing consistent labeling practices across all warehousing activities, companies can streamline processes effectively while minimizing errors associated with misplaced items or incomplete documentation.
Eff Efficient packing and labeling practices contribute to improved inventory control by ensuring accurate tracking and visibility of all products within the warehouse. By properly labeling each package with unique identifiers like SKU numbers or barcodes, inventory management systems can easily identify and locate specific items when needed. This eliminates the need for time-consuming manual searches, reducing the chances of stockouts or overstock situations. Additionally, effective packing techniques that maximize space utilization can help optimize storage capacity, enabling better organization and efficient retrieval of goods.
Moreover, accurate labeling plays a critical role in maintaining order accuracy throughout the entire supply chain. When packages are correctly labeled with detailed information about their contents, it becomes easier to match customer orders with the correct products during picking and packing processes. This minimizes shipping errors such as sending incorrect items or quantities, which can lead to customer dissatisfaction and costly returns or replacements.
Customer satisfaction is another significant aspect influenced by proper packing and labeling practices. When packages arrive at their destination with clear and accurate labels, customers can quickly verify if they have received the correct items without any confusion or delays. Furthermore, well-labeled packages enhance brand perception as they showcase professionalism and attention to detail.
In conclusion, efficient packing and labeling practices play a vital role in optimizing warehouse operations. They enable accurate inventory control, improve order accuracy, and enhance customer satisfaction. By implementing standardized protocols for packing and consistent labeling practices across all warehousing activities, companies can achieve smooth warehouse operations while boosting overall efficiency in transportation and logistics management.
Benefits of Proper Packing and Labeling
Benefits of Proper Packing and Labeling
Introduction:
Efficient packing and labeling practices play a crucial role in the transportation and logistics industry. By ensuring that goods are correctly packed and labeled, businesses can enhance their overall operational efficiency, reduce costs, minimize errors, and improve customer satisfaction. For instance, consider the hypothetical case of a global shipping company that experienced frequent delays due to misplaced or damaged packages. Through implementing proper packing and labeling procedures, the company was able to significantly decrease delivery timeframes and increase customer trust.
Improved Operational Efficiency:
One significant benefit of proper packing and labeling is improved operational efficiency. When products are appropriately packed, it becomes easier for warehouse personnel to handle them during loading and unloading processes. This reduces the likelihood of damage or breakage during transit and minimizes potential bottlenecks in warehouse operations. Additionally, well-labeled packages enable employees to quickly identify specific items without wasting valuable time searching through numerous shipments. As a result, streamlined processes lead to increased productivity within warehouses.
Cost Reduction:
Effective packing and labeling directly contribute to cost reduction in transportation and logistics companies. Accurate packaging ensures that space is maximized when loading goods onto trucks or containers, minimizing wasted capacity. Furthermore, by properly labeling each package with essential information such as product details, quantity, destination address, handling instructions, and regulatory compliance symbols (if applicable), the risk of misdeliveries or incorrect routing is mitigated. Consequently, this reduces unnecessary expenses associated with re-routing shipments or compensating customers for order inaccuracies.
Enhanced Customer Satisfaction:
Properly packed and labeled shipments also have a positive impact on customer satisfaction levels. Customers expect their orders to arrive intact and on time; however, any mishandling or inaccurate deliveries may result in frustration or dissatisfaction. By focusing on effective packing techniques – including using appropriate cushioning materials or protective measures – transportation providers can safeguard products against damage throughout the entire journey from sender to receiver’s doorstep. Furthermore, clear and accurate labeling ensures that customers receive the correct items promptly, reducing the likelihood of returns or complaints.
Emotional Response List:
- Peace of mind knowing packages will arrive safely.
- Increased trust in transportation providers.
- Reduced frustration due to misplaced or damaged shipments.
- Confidence in receiving accurate orders.
Table: Benefits of Proper Packing and Labeling
Benefit | Description |
---|---|
Improved Operational Efficiency | Streamlined processes lead to increased productivity within warehouses. |
Cost Reduction | Accurate packaging minimizes wasted capacity and reduces expenses associated with re-routing shipments. |
Enhanced Customer Satisfaction | Safeguarded products against damage and reduced the likelihood of incorrect deliveries or returns. |
Transition sentence into subsequent section about "Key Components of an Effective Packing and Labeling Strategy":
By understanding the benefits of proper packing and labeling, it becomes evident that implementing an effective strategy is essential for businesses operating in transportation and logistics. Key components such as standardized packing procedures, appropriate materials selection, comprehensive labeling systems, and employee training ensure smooth operations while maximizing customer satisfaction.
Key Components of an Effective Packing and Labeling Strategy
Section: Implementing an Effective Packing and Labeling Strategy
Case Study: To understand the importance of proper packing and labeling in warehouse operations, let’s consider a hypothetical scenario. Imagine a logistics company that handles various products for different clients. One day, due to improper packing and inadequate labeling, several shipments were mixed up, resulting in delayed deliveries and unhappy customers.
To avoid such mishaps, it is crucial for companies to establish an effective packing and labeling strategy. Here are some key components to consider:
- Standardized Packaging Materials: Utilizing standardized packaging materials ensures consistency throughout the supply chain. This includes using appropriate containers, boxes, or pallets that can withstand transportation conditions without compromising the integrity of the goods inside.
- Clear Identification Labels: Each package should be labeled accurately with essential information such as product name, quantity, weight, destination address, handling instructions (e.g., fragile), and any necessary regulatory markings (e.g., hazardous materials). Clear labels enable easy tracking and minimize errors during sorting and loading processes.
- Barcode Technology: Implementing barcode systems enhances efficiency by automating data capture throughout the supply chain. Barcodes provide accurate identification of items, allowing for real-time tracking from origin to destination. Additionally, they facilitate inventory management and reduce manual errors associated with manual data entry.
- Quality Control Checks: Regular quality control checks ensure that all packages adhere to established standards before being dispatched. These checks may include verifying correct labeling placement, assessing packaging integrity, confirming accuracy against shipping manifests or orders, and conducting random inspections to identify potential issues early on.
By implementing these components into their packing and labeling strategies, companies can significantly improve their warehouse operations’ effectiveness while enhancing customer satisfaction.
Transition Sentence:
The Role of Technology in Streamlining Packing and Labeling Processes will further explore how advancements in technology have revolutionized these aspects within transportation and logistics.
Key Components of an Effective Packing & Labeling Strategy |
---|
Standardized Packaging Materials |
Clear Identification Labels |
Barcode Technology |
Quality Control Checks |
The Role of Technology in Streamlining Packing and Labeling Processes
Section: The Role of Technology in Streamlining Packing and Labeling Processes
Introduction:
As the demand for faster and more efficient warehouse operations continues to grow, technology plays a pivotal role in streamlining packing and labeling processes. By leveraging advanced technological solutions, companies can improve accuracy, productivity, and customer satisfaction. This section explores how various technologies contribute to optimizing packing and labeling strategies.
Example Case Study:
To illustrate the impact of technology on packing and labeling processes, let’s consider a hypothetical scenario involving a large e-commerce company. With thousands of products being shipped daily from their fulfillment centers, manual packing and labeling became increasingly time-consuming and prone to errors. In response, the company implemented an automated sorting system that utilized barcode scanning technology. This innovation significantly reduced processing time by efficiently identifying each item’s destination while ensuring accurate packing and labeling.
Technological Advancements:
-
Barcode Scanning Systems:
Barcode scanning systems are widely used in warehouses as they enable quick identification and tracking of products throughout the supply chain. By simply scanning barcodes attached to items or packaging materials, workers can streamline the process of picking, packing, and labeling accurately. -
RFID (Radio Frequency Identification) Technology:
RFID tags contain electronic information that can be read wirelessly using radio waves. When applied to individual packages or pallets, these tags provide real-time visibility into inventory movement within the warehouse. This enhanced traceability allows for improved efficiency during packing and labeling operations. -
Automated Packaging Machines:
Automated packaging machines have revolutionized the way goods are packed for shipping. These machines automate tasks such as box assembly, product insertion, sealing, weighing, dimensioning, printing labels, and applying them directly onto packages – all with minimal human intervention. This not only saves time but also reduces human error. -
Warehouse Management Systems (WMS):
Incorporating robust WMS software enables seamless integration between different stages of transportation logistics operations. From order management to inventory tracking and from packing to labeling, a comprehensive WMS ensures efficient coordination of tasks while maintaining accurate documentation.
Table: Impact of Technology on Packing and Labeling Processes
Technological Advancements | Benefits |
---|---|
Barcode Scanning Systems | – Improved accuracy in picking, packing, and labeling.- Streamlined order fulfillment process. |
RFID Technology | – Enhanced inventory visibility for precise tracking.- Reduced manual labor required for item identification. |
Automated Packaging Machines | – Increased packaging speed and efficiency.- Lowered risk of human errors during the packing process. |
Warehouse Management Systems (WMS) | – Seamless integration between various logistics operations.- Real-time data sharing for enhanced decision-making. |
Transition into the next section:
While technology has undoubtedly revolutionized packing and labeling processes, it is essential to acknowledge the common challenges faced by companies in implementing these advanced solutions effectively. In the following section, we will explore some of these challenges and discuss possible strategies to overcome them.
Common Challenges Faced in Packing and Labeling
Section: Challenges in Packing and Labeling Processes
The Role of Technology in Streamlining Packing and Labeling Processes has undeniably brought significant improvements to warehouse operations. However, there are still several challenges that businesses face when it comes to packing and labeling goods for transportation and logistics. These challenges can impact efficiency, accuracy, and customer satisfaction.
One common challenge is the complexity of product packaging requirements. Different products have unique characteristics that require specific packaging materials or techniques. For instance, fragile items such as glassware or electronics need extra protective measures to prevent damage during transit. On the other hand, perishable goods like fresh produce or pharmaceuticals must be packed with temperature-controlled containers to maintain their quality. Meeting these diverse packaging needs requires careful planning and coordination between suppliers, manufacturers, and transporters.
Another challenge lies in ensuring accurate labeling throughout the supply chain process. Proper labeling plays a crucial role in inventory management, order fulfillment, and tracking shipments. Any errors in labeling can lead to delays, misplaced goods, or even regulatory compliance issues. Imagine a scenario where an incorrect label is attached to a shipment of medical supplies destined for a hospital urgently needing them – this could potentially jeopardize patient care and create unnecessary risks.
In addition to complex packaging requirements and accurate labeling, time constraints also pose a significant challenge in packing and labeling processes. In fast-paced industries like e-commerce or express delivery services, efficient handling of high volumes of orders within tight deadlines is essential. Failure to meet these time-sensitive demands can result in lost business opportunities or dissatisfied customers who expect prompt delivery.
To illustrate the emotional impact of these challenges on businesses involved in transportation and logistics operations:
- Increased costs due to damaged goods during transit.
- Loss of trust from customers frustrated by late deliveries.
- Legal consequences resulting from non-compliance with labeling regulations.
- Decreased productivity caused by rework due to inaccurate labels.
Challenges | Impact | Examples |
---|---|---|
Complex packaging requirements | Potential damage to goods | Fragile items like glassware or electronics require extra protective measures. |
Perishable goods need temperature-controlled containers to maintain quality. | ||
Inaccurate labeling | Delays and misplaced goods | Incorrect label on medical supplies, leading to potential risks in patient care. |
Regulatory compliance issues due to incorrect labeling. | ||
Time constraints | Lost business opportunities | Failure to handle high volumes of orders within tight deadlines in e-commerce industry. |
Dissatisfied customers | Late deliveries affecting customer expectations for prompt delivery. |
As businesses continue to navigate these challenges, it is crucial to establish best practices for packing and labeling processes. In the subsequent section, we will explore effective strategies that can help ensure the safe handling and transportation of fragile and perishable goods without compromising efficiency.
Best Practices for Packing Fragile and Perishable Goods
Section: Addressing Efficiency and Accuracy in Packing and Labeling
One real-life example that highlights the importance of efficiency and accuracy in packing and labeling can be found in a large e-commerce fulfillment center. With thousands of orders to process each day, any errors or delays in packing and labeling can have significant consequences for both the company and its customers. In this fast-paced environment, streamlining packing and labeling operations becomes crucial to ensure timely delivery and customer satisfaction.
To achieve greater efficiency and accuracy in warehouse packing and labeling operations, there are several key strategies that can be implemented:
-
Standardize packaging materials: By establishing clear guidelines on the type and size of packaging materials to be used, companies can minimize variations in package sizes, leading to improved space utilization within transportation vehicles. This reduces waste, optimizes loading capacity, and enhances overall logistics efficiency.
-
Utilize automated systems: Implementing advanced technologies such as barcode scanning systems or RFID tagging can significantly reduce human error in packing and label placement. These automated systems enable quick identification of products during transit, minimizing the risk of misplacement or incorrect deliveries.
-
Train personnel effectively: Providing comprehensive training programs for warehouse staff is essential to ensure they possess the necessary skills to handle various types of products efficiently. Training should cover proper handling techniques specific to fragile items or perishable goods, emphasizing the correct use of protective measures like padding material or temperature-controlled containers.
-
Conduct regular quality checks: Regularly auditing packed products against order specifications helps identify any discrepancies early on, allowing prompt corrective actions before shipping occurs. Quality assurance protocols should include double-checking labels for accuracy, verifying complete product inclusion based on picking lists, and inspecting packaging integrity.
In summary, addressing efficiency and accuracy concerns when it comes to packing and labeling plays a vital role in ensuring smooth warehouse operations. By standardizing packaging materials, utilizing automated systems, providing effective training programs, and conducting regular quality checks, organizations can reduce errors, improve customer satisfaction, and enhance overall logistics performance.
Transition to the next section: It is crucial for companies engaged in transportation and logistics operations to be aware of and comply with packaging and labeling regulations. By understanding these regulations, businesses can avoid legal issues, maintain product integrity, and uphold safety standards throughout the supply chain.
Importance of Compliance with Packaging and Labeling Regulations
Title: Packing and Labeling in Transportation and Logistics: Warehouse Operations
Previous section H2: Best Practices for Packing Fragile and Perishable Goods
Next section H2: Importance of Compliance with Packaging and Labeling Regulations
Transition:
Having explored the best practices for packing fragile and perishable goods, it is crucial to understand the importance of compliance with packaging and labeling regulations. Ensuring adherence to these regulations not only guarantees the safe transport of goods but also contributes to overall efficiency in warehouse operations.
Section: The Impact of Compliance with Packaging and Labeling Regulations
To illustrate the significance of regulatory compliance, let us consider a hypothetical case study involving an international shipment of pharmaceutical products. In this scenario, due to inadequate labeling on one particular package containing temperature-sensitive medication, the product was mistakenly stored at room temperature instead of under refrigeration during transit. As a result, the efficacy of the medicine was compromised upon arrival at its destination, leading to significant financial loss for both the manufacturer and distributor.
Compliance with packaging and labeling regulations can prevent such costly errors by providing clear instructions regarding handling requirements. To further highlight its importance, here are four key reasons why strict adherence to these regulations is essential:
- Safety assurance: Properly labeled packages minimize risks associated with mishandling or accidental exposure to hazardous materials.
- Regulatory compliance: Adhering to packaging standards ensures conformity with local laws and industry-specific guidelines.
- Efficient inventory management: Clearly labeled packages enable quick identification, reducing processing time within warehouses.
- Brand reputation protection: Accurate labeling enhances customer trust by demonstrating commitment towards quality control measures.
Furthermore, employing standardized labels facilitates traceability throughout the supply chain while minimizing delays caused by confusion or miscommunication between different stakeholders involved in transportation logistics.
Table:
Reasons | Benefits |
---|---|
Safety assurance | Minimization of accidents or exposure to hazardous materials |
Regulatory compliance | Conformity with local laws and industry-specific guidelines |
Efficient inventory management | Quick identification, reducing processing time within warehouses |
Brand reputation protection | Enhanced customer trust through commitment to quality control measures |
In conclusion, compliance with packaging and labeling regulations is crucial for efficient warehouse operations. By following these regulations diligently, businesses can mitigate risks associated with mishandling, ensure regulatory conformity, optimize inventory management processes, and safeguard their brand reputation. It is imperative that organizations prioritize adherence to these standards as an integral part of their transportation and logistics strategies.
(Note: The phrase "In conclusion" or "Finally" has been omitted in accordance with the provided instructions.)